I live near one of the largest copper mines on earth (Kennecott Utah Copper - KUC). I helped manage a smaller copper mine for 8 years. Observation: Wind/Solar/Battery Proponents & ESG bean-counters are completely out of touch with copper mining & production.
Civilization’s very first metal was copper. Though eventually surpassed in importance by iron and steel, with with Edison and Tesla, world demand for copper became nearly infinite. Butte, MT held the world's highest-grade copper resources. And the whole world came to Butte to mine copper.
Several lines of my family converged in Butte from as far away as Croatia, Cornwall, and North Carolina - to mine copper. My grandparents met there during WW2 (grandpa was at the USN Officer Training School, School of Mines). My mother was born in Butte. I know a thing or two about it.
The so-called energy “transition” (energiewende) is a copper monster. The resulting demand for copper far exceeds anything the world has ever seen before—even during the electrification heyday (1870 onward).

Solar power systems use abt 5.5 tons of copper per MW (heat exchangers of solar plus wiring and cabling that transmits the electricity in PV cells). 262 GW of new solar installations between 2018 and 2027 in North America alone = 1.9 billion lbs. of copper.
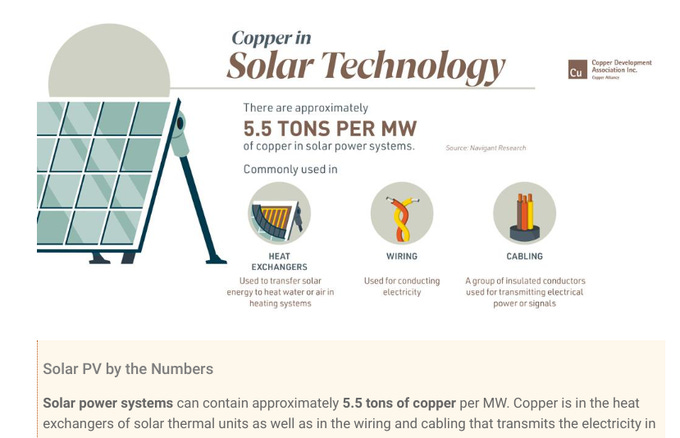
Put on a hospital gown because we're going under the scalpel for the biggest unnecessary medical procedure in history. Here's the new and totally unnecessary interstate transmission system that's going to cost ratepayers billions for garbage power we don't need. /16 Source: S&P Commodity Insights
Copper mining starts with drilling. Drill rigs runs on diesel fuel. And they burn a lot. In copper mines, fleets of drills run in shifts, often 24/7. The drills require tires, lubricating oil, grease, dust control systems, and sophisticated electronics, maintenance, etc.
Strip Ratio means the number of waste rock benches that need to be drilled, blasted, loaded, hauled, and dumped, compared to the number of ore benches the stripping will open up. Strip ratios vary widely from mine to mine and phase to phase. Strip can be as high as 15.5:1.
The strip ratio at volcanic massive sulfide deposits like Kennecott are usually above 5:1. And that means lots of tungsten oxide drill bits. The lifecycle assessment for tungsten oxide production is not pretty. It's mostly made in China, home of hundreds of coal power plants.
Larger patterns usually work for waste but ore needs crushing, so drill patterns are tighter. Regardless, copper mining means drilling lots of holes through hard rock. It can take weeks or months to drill out a single bench (a defined block in the pit). https://rpmdrilling.co.za/blast-hole-drilling-process/…
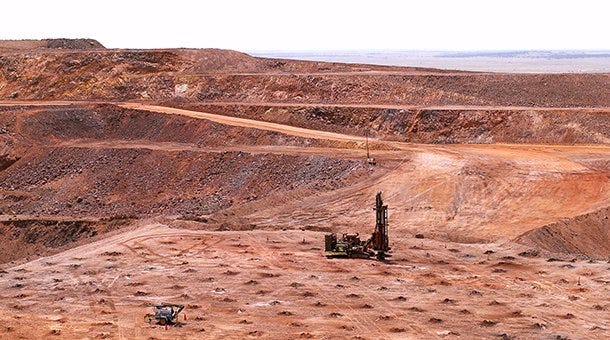
Then comes the fun part: blasting. Ammonium Nitrate / Fuel Oil -ANFO- is the primary blasting agent. It's 94% ammonium nitrate with diesel fuel oil. AN is manufactured from methane and requires a great deal of fossil fuel energy and associated emissions.
It is not coincidental that the Nobel Prize carries that name. Alfred Nobel's weird trick (dynamite) altered the course of humanity in countless ways, from War, to the petro-chemical industry, to mining.
Each tire weighs 12,000 pounds and is made with nearly 100% petro-chemical feedstocks (hundreds of ingredients) and 100% fossil energy. Black=carbon black. Tires are not recyclable. And they don't last that long. Kennecott has its own tire landfill.
Steel to manufacture the equipment; tires; lubricating oil; grease; fuel; maintenance; batteries; wear steel; moving things around the world (importing trucks from Korea), mobilization, and demobilization - 100% consumptive just to drill, blast, pick up, and move rock.
Ore has to be crushed. The scale of this equipment is hard to describe. The fossil fuel and other inputs that went into this single crusher in one copper mine - and associated CO2 and other impacts - much less the power to run it - are enormous. Constant maintenance- replacement.
A childhood friend of mine has been a Kennecott equipment operator for decades. These trucks consume some 92 gallons of diesel fuel every hour, whether they're moving or not. Kennecott has a fleet running 24/7/365.
Next, milling & grinding. Sulfide ore is hard and must be milled down to a fine sand. Each ball/SAG mill is rated in thousands of horsepower (a single ball mill = 16k HP). Can't mill ore with weather-power. Mills operate 24/7/365.
We aren't even close to being done. After milling and grinding, the ore must be concentrated and tailings floated. At Kennecott, this requires pumping millions of gallons of water slurry many miles, requiring enormous quantities of dependable electrical energy (coal-gas).
Tailings are concentrator waste. The Kennecott tailings pond enormous. Its construction to date has required moving billions of tons of soil, rock, clay, and engineered cover (tens of millions of tons of processed, washed, screened, and imported sand and gravel).
It would be impossible to accurately quantify, today, the true fossil fuel requirements associated just with this one impoundment, its construction, maintenance, and reclamation. We won't know for years yet its final size / configuration. Reclamation is DECADES in the future.
Concentrates (24% Cu) are smelted using COAL. No other fuel will do. Sulfide ore is high in sulfur, making KUC an important sulfuric acid producer. Acid is sold for mining other (acid soluble) copper and uranium, making phosphate fertilizer, and other processes.
The ore at KUC is sulfide—not acid soluble. But the ore at the mine I helped manage is heap-leached very efficiently using KUC acid derived from sulfide ore. Industrial operations are efficient and symbiotic.
During smelting, the concentrates turn to “lava” and self-separate based on elemental specific gravity. Silica sand and other fluxing minerals form a “froth” at the top and are tapped/removed to form slag. Metal values from the smelter are then removed.
We still have a ways to go. Purification and separation of smelted metals and other valuable byproducts requires many more steps. Volumes have been written about KUC, one of the world’s most important mineral sources. This thread is an extreme oversimplification.
For copper, the process is Electrowinning. Metal values are dissolved in H2SO4 and then plated out in to form CATHODE plates. This step consumes vast quantities of electrical energy. TO BE SURE, because it is CHEAP, EW plants often utilize wind-solar power (e.g. load shedding).
The fact that mining companies use load shedding agreements to soak up excess, garbage power is not a compliment. It's because the value of wind-solar to the grid is so low that utilities have to pay to get rid of it.
The end result of the entire mining process is new cathode copper. I directly challenge analysts calculating lifecycle impacts of wind-solar-batteries to account for the fossil fuel and carbon impacts expended in producing new cathode copper. 100% consumptive.
Only the best, highest-quality (purity) copper cathode meets the specs for generators like those used in wind turbines. The wire must be rolled thin and long; any imperfections in the cathode result in broken wires. Turning cathode into wire requires yet more FOSSIL ENERGY. Cathode is shipped from the mine to a rod mill (sometimes thousands of miles, including interim warehousing). At the rod mill, it's melted in an electric arc furnace (dispatchable power). Can't run an EAF on solar. 99.9% purity virgin cathode is prized by rod mill buyers. Wire gauge (thickness) governs resistance and other technical factors involving all generators. The thinner the wire, the more energy required and the higher the purity of the feed. Limited high-quality scrap can be used.
COPPER ORE GRADES: Copper sources have driven humanity since prehistoric times, especially Iberia and Cornwall. Advanced Roman metallurgy allowed them to flourish. One of my family lines came to Butte, MT from Cornwall - to mine copper. His Cornish ancestors dated to the Romans.
Since Roman times, copper ore grades have been decreasing, astronomically so since Edison's and Tesla's inventions electrified the planet. This is a function of the natural occurrence of copper in earth's crust and the cost of extracting it. Commodity economics. BUTTE:
There are only 23 mines in the USA mining copper. The largest is Kennecott, which has large volumes of low-grade ore. Daniel C. Jackling was the first to figure out how to use large-scale equipment to get the low-grade to pay. Current ore grade reserves at KUC are 0.47%. Why does grade matter? The essential CARBON energy required to extract one pound of copper cathode go up as grade decreases. Today's ore was yesterday's waste rock. BTW, Jackling's breakthrough? The COAL-powered steam shovel.
BHP, the world’s third largest copper producer, estimated that grade decline could remove about 2 million metric tons per year (mt/y) of refined copper supply by 2030, with resource depletion potentially removing an additional 1.5 million to 2.25 million mt/y by this date.
The only way to produce the same tons of Cu per year is to mine and process even that much more ore and strip that much more waste. Hard to believe you can't mine and process copper with windmills and solar panels. You need OCEANS of Petroleum, coal & such.
TO BE SURE, our ability to be able to economically recover copper from increasingly-declining grades of ore is a modern marvel, driven nearly 100% by ABUNDANT, CHEAP CARBON ENERGY. But declining grades are just a throughput issue. More mining; more hauling; more tailings etc.
The so-called energy “transition” is expected to DOUBLE the world demand for COPPER in the next 10 years. As large as it is, KUC only supplies 1% of world copper demand. FANTASY: the world will create 100 MORE KUC-scale operations in a decade.
The World's large porphyry copper deposits are all known and most have been depleted or are nearing depletion, including KUC. Declining ore grades explain the vast impact footprints (Peru depicted).
But new demand will NOT result in a copper shortage, rather a shortage of AFFORDABLE copper. Copper will simply inflate till its cost matches copper’s next most economical substitution: ALUMINUM. https://windpowerengineering.com/aluminium-as-a-conductor-material-a-lighter-and-more-economical-alternative/
Aluminum is a good conductor albeit with different properties and limitations (such as electric motor windings - Al is too brittle). Al is already used for wires. The primary impediment is simply cost. Compared to copper, production of Aluminum requires EVEN MORE COST AND CARBON
Al has 61 percent of the conductivity of copper, but has only 30 percent of the weight but both can be used in many applications. Substitution is happening and will continue to happen. BUT that does not mean Al has a lower carbon footprint.
ALL of the copper mined on earth prior to wind/solar energy was essential to civilization for uses unrelated to wind/solar. Copper requirements will continue and will even expand with technology development. INFLATING the cost of copper to match aluminum harms civilization.
IF Aluminium were better than copper, civilization would have already switched.
SO, doubling the demand for conductive metals will just result in INFLATION. Everything electric will just cost that much more. Inflation PRODUCTION Act much?
Yet, affordable copper abundance is simple. A single high-grade copper mine can change the world (such as Iberia and Cornwall for copper/tin and Petosi, Bolivia for silver). Thank Mother Nature. And the USA has two: Resolution Copper in AZ and Pebble in Alaska.
Resolution is one of the largest undeveloped copper projects in the world and has the potential to quite quickly become the largest copper producer in North America. The Resolution resource is high-grade, vast, and deep underground. NO OPEN PIT
Remember, high grade ores mean the LOWEST CARBON FOOTPRINT. So, naturally, the same groups frantic to stop Climate Change via massive deployment of wind/solar/batteries SUPPORT the opening of such a rare, world-class, high-grade copper resource. Well, not so much.
It's hard to describe the internal amusement I experience every time a Wind/Solar/Battery advocate lectures me about the imminent depletion of uranium and thorium, while ignoring tiny details like COPPER and the perpetual CARBON ENERGY it requires. Windmills Forever!.
Fortunately for humanity, there is a far better solution that will not require any increase to normal worldwide mineral production rates nor result in mineral inflation. Its net-net fossil fuel inputs are de-minimis. That solution is nuclear power (fast reactor is + 27x)
In the '70s world energy crisis, France overbuilt and had to scramble to find buyers and to electrify everything. That's real economic growth. Imagine that! Abundant, affordable energy FIRST; electrify everything SECOND. Today it's energy poverty first then electrify nothing.
For more information, I highly endorse @MarkPMills podcast on the mineral requirements and other real-world implications of energy, wind/solar/batteries:
The Last Optimist on Apple Podcasts
I also endorse @DecoupleMedia and the outstanding work of @Dr_Keefer, including several episodes with Mark P. Mills.
Decouple - Magical Thinking, Moore's Law, and Energy feat. Mark P Mills
8:26 PM · Oct 23, 2022·Twitter Web App
The first COPPER thread devolved into a mostly unproductive debate about the recycleability of copper (it is recyclable but there's a serious contamination limitation + new CARBON), the image on the first post, aluminum, and such. Recycling: